3400kW Solar Project for Washington Gas, Southbridge, Ma. Landfill Site
Project Data:
End-User: Washington Gas
Installer: Martifer Solar USA
Location: Southbridge, Ma.
Date of install: April 2013
Size of system in kW: 3400kW
Energy produced since installation: approximately 9,800MWh as of 2/2015
Special Challenges Met: Shallow soil conditions were not anticipated by the EPC design team
Project Brief:
John Millard was hired by Martifer Solar in November of 2012 to manage four utility scale solar projects in New England, the Maynard Landfill Solar project was one of these projects.
Millard hired the the four project teams that would execute the four designs produced by Martifer Solar USA project engineers in LA. Millard oversaw the design of each project and managed the production of construction documents for each design except for the Southbridge project which had already been designed by the time of his joining Martifer in November 2012. Of the four solar projects, three of the projects were located on landfill sites. The Maynard Massachusetts project and the Brookfield Massachusetts project both required designs that would not penetrate the landfill. This required that all electricity distribution for the solar project would utilize code compliant cable tray design and self ballasted mounting hardware for the solar support structure. s was discovered at the Southbridge Massachusetts project, New England soils are typically shallow and represent hard dig conditions. Application engineers ignore this fact of life at their peril.
In the case of the Southbridge Massachusetts project, soil depth issues were already preventing extensive trenching to code-compliant depth across the 3.4 MW Solar project construction site. One of the first corrective actions that Milard was responsible for implementing was a change order that solved for the failure to place over 500 lineal feet of DC conductors in code compliance trenches. The solution was to create concrete duct bank that would lie on top of the shallow hardpan and deliver the PVC conduit from the combiner boxes to the inverter pads. This change order required extensive field measurements and coordination with the engineers in LA in order to institutes a properly documented change.
With the Brookfield and Maynard projects, both landfill projects with restrictions from penetrating the landfill cap, Millard was able to incorporate cable trays into the design for these two projects prior to the start of construction. This enabled the designers to freely distribute DC electrical power where ever it was possible to site self ballasted solar support structure on top of the landfill. This also enabled the designers to reduce the size of the electrical conductors due to the fact that they were air cooled in the cable tray according to national electric code. Other benefits to using cable tray are described in the memo below:
Re: Coordination of Cable Management with Geotech Report...
A learning opportunity is evolving here on the East Coast that will serve us well. Without being too project specific, the challenges experienced here will touch every department in the company.
As a newcomer to Martifer, and aware of the “hindsight is 20 / 20” rule, making observations about decisions taken by presdescessors is a luxury. Now that I am one of the decisionmakers on these projects, vulnearble to making decisions on the fly that appear to make me look like a good “multi-tasker” when in reality, I may be making a hasty decision that costs- and costs dearly.
Therefore, a quality control process known as a “peer review” is an opportunity for a second set of eyes to scan the drawings for design decisions that may have been made hastily (prior to contract award). Decisions such as carte blanche trenching to distribute DC wiring: many ground mounted projects will sustain hundreds of metres of trenching for this purpose. Has anyone asked the question why we always trench? Here are some downsides to trenching:
Heavy equipment rental costs & dangers, Spoils may contaminate topsoil, Labor to trench is $4.25 - $4.50 / LF, Unforeseens in the ground pose risks, Passing these risks onto contractor is costly., Conduit must be purchased with all attendent fittings, couplings, expansion jts, etc., Resistivity calulations are more heat intensive resulting in more Copper / Aluminum due to heat premium, More length requ’d to transition in / out of ground, More length- more pipe, more labor, more IR loss, More permit risk of env. cost (stockpiling farm soil), Open Trenches restrict movement of site ops, Restrictions of movement cost time / create danger, Erosion issues, Additional OSHA triggers, Landscaping repairs, costs, requirements by AHJ, Difficult to access/ change or repair, Leaks Water/ Damages Cable, The following memo is an illustration of how a project in New England- a place with shallow rocky soil can surprise the veteran PV designer with setbacks that exponentially revise up costs and duration. The Pilgrims and the origins of the Thanksgiving Holiday are truths to be told, Future landfill projects here in New England will dictate that all wire management occur above grade. There will be no trenching on these projects allowed per SEPA. Now is the time to explore options to “trenched earth”, Crystalized: if the Geotech report says there is no soil for a 24” deep trench, find another method of distributing wires around your solar project.
Challenge Statement: Designers under extreme pressure to print construction issues sometimes make mistakes. These mistakes have to be rectified on site by project managers and construction managers without the benefit of quick decision making processes available to designers- rather than rectifying some vector graphics and text blocks on a cad drawing, PMs & CMs have their sub-contracted partners on the project uncovering unconstructible designs and submitting RFIs, and Change Orders after careful study of the problem. The the Martifer CM / PM team have to convince Design Staff that there is a constructibility problem with the drawing. Depending on the disposition of the designer, the process of realizing the problem can take a while to acceptance.
Once the designer has accepted the constructiblility challenges of the original construction plan or detail, there is the solution phase. This phase may not take place quickly or, worse, there may be a delay to the solution for all kinds of other reasons related to change process within Martifer or related to the reluctance to initiate change by other parties in the internal change process. Many times the designer who has accepted the original “mistake” may find acknowledging the original “mistake” as an occuptional hazard and delay or distract the processing of the change.
This memo looks at a specific technical issue related to underground surprises. The observations made on site have concluded that the original design was not constructible, and there are photographs that show a soil dept that makes it clear- a code compliant conduit trench was indeed not possible to be constructed at this site without the use of dynamite. Pick axes, sledge hammers and pneumatic hammers would not prevail in the conditions at this site in order to deliver the original detail that was drawn on a piece of paper. Some have suggested that the electrical contractor should have detected these conditions in the Geotechnical Report. The good news is that the mounting hardware designer must have, as clearly evidenced by the large, precast concrete ballast blocks:
While using this “Braille” approach to discovering the extent of the shallow soil, constuction continued at breakneck pace on all aspects of the design, including the inverter pads- The PM & CM were communicating their findings to Martifer and seeking guidance on the solution to this problem of how to cover the conduits for DC distribution on the east side of the site with a code compliant amount of cover...
The electrical contractor immediately recommended cable tray to the PM. This suggestion was rejected by Martifer and another solution was proposed- concrete duct bank. This would be cast over the pvc conduits and covered with clear fill. The PM was instructed to obtain a bid for the placement of at least 4” of cast-in-place concrete over the top of the concduit. But how much shallow conduit would be manually determined to require this solution to accurately describe the scope and quantity of the concrete? The trencher had to keep trenching and inspections for shallow trench conditions would have to be made before a drawing that showed the extent of the shallow conditions could be issued to the concrete contractor. This process took a great deal of time.
As construction continued, new shallow soil challenges emerged such as how to transition from conduit in the proposed concrete duct bank into the inverter since the inverter pads also sat on shallow soil conditions. The drawings had called for bottom entry of the conduits into the DC recombiner and the AC compartments in the inverter. Unfortunately, the concrete ductbank solution for the conduits assumed that the conduits would eventually find their way to deeper soil and consequently to the inverter pad, where they would dive under the pad and emerge through the bottom entry in the inverter. This was not to be the case...another constructibility issue requiring a change order.
Pad details show bottom entry to inverter from trench...
Now that the conduits are to be encased in concrete on the surface of the hardpan, and the inverter pad also sits on the surface of the hardpan, there is no way for the conduits to transition up, into the inverter recombiner through the inverter pad for two reasons;
They are at the same level as the bottom of the slab.
Unless the slab is built up with hundreds of yards of concrete in order to allow sufficient height for the 90 degree transitions to occur under the slab, the conductors have no way to get into the DC compartment nor is there room for the AC conductors to egress the AC compartment to leave the pad and reach the adjoining MV Transformer with a similar bottom entry:
How to stub up in shallow soil condition?
Now the PM / CM team on site see the limitations of the concrete encased conduits as far as: how to enter the inverter? Side entry seems likely, but how to transition out of the duct bank to enter the side of the inverter? If they had adopted the cable tray solution presented by the electrical contractor, they would have avoided a great deal of shallow trenching, wire pulling and now concrete encasing. Had tray been adopted, there would still have been concrete duct bank required for maintenance vehicular circulation over the wire runs.
Cable Tray is the more flexible solution for utility scale:
Transition from tray into conduit for vehicle over passes...
Cable Tray is used in many projects where its flexiblility, cost, ease of access to conductors, labor friendliness and tendency to allow other more flexible solutions to other challenges such as combiner box locations, wire transitions from mounting hardware into combiner boxes and inverters with side entry opportunities.
Cable Tray side entry capability for inverter service...
On utility scale projects where agricultural land is environmentally protected, local zoning committees are reluctant to permit multi-MW projects because of the damage that extensive trenching causes to the top soil. In some cases they have required topsoil to be scraped off the surface of the ground to a depth of 12 “ and stockpiled, only later to be re-distributed by the civil contractor after the trenching has completed the process of backfilling the spoils into the trenches. Needless to say this is an expensive additional cost of trenching:
Environmentally protected farmland is often topsoil focused and costly topsoil management is triggered by trenching when this could be avoided by using cable tray.
Use of cable tray eliminates 95% of trenching, conduit, and equipment required to excavate trenches. In fact, at nearly $5 per foot, these eliminations from the construction budget must be subtracted from the cost of tray which typically amounts to $5 to $10 per linear foot. The cost of pulling wire may be equated to the cost of laying wire in tray, but in fact, pulling wire is much more labor intensive than tray layout. There are other savings to be had with cable tray- and that is the savings in copper that there is to recover when applying the open air thermal resistivity coefficient to PV wire sizing- both for home uns to boxes and for larger conductors returning to DC recombiners. Tray provides a valuable route to which small control power conductors in conduit can be clipped onto the side of tray in order to separately deliver AC power to devices on the inverter pad, tracker motors or security devices.
NEMA 3R HOFFMAN BOXES W 12 CIRCUITS EA MOUNTED ON THEIR BACKS ON TRAY AND INSPECTED ALL DAY LONG...
There is of course, the opportunity to mount combiner boxes on tray and that savings over free standing vertically mounted boxes is equal to the full value of all concrete, excavation, and strut assemblies which amount to several hundred dollars per box. (not to mention the loss of conduit, elbows, couplings and labor associated with stubbing up.
Side Entry Service for Inverters is accessible and saves a lot of subslab coordination, setting out, and mess on site...
The back mounting of combiner boxes on tray is an electrician’s idea. The transitions from tray to box requires only a minute devation of angle for a Sealitite segment to steer conductors right through the side of the box, into the fuse holders, terminal blocks and grounding lugs. Grounding is easy with tray since the tray itself is used as a grounding conductor provided that jumpers are installed at each tray splice.
TYPICAL TRANSITION FROM MOUNT TO TRAY...NO PIPE
The proximity of back mounted boxes to their respective source circuits, by nature, minimizes wirelength, improves efficiency of the system design and costs less for copper. The access to the box is from the top and allows for direct skylight to illuminuate the interior of the box. With the door sealed properly with a neopreme weather strip, NEMA 3R boxes are permissible where a NEMA 4 box might otherwise be called for.
ELECTRICIANS ROUTINELY INSTALL BOXES ON THEIR BACKS
The Cable Tray acts as a bi-directional super highway for DC conductors to travel from source circuits to combiner boxes and from combiner boxes to inverter DC recombiners. Tray also is usefull for projects where there is a non-whole number of strings in a row of modules and a jumper is neccessary to complete a string. That jumper can ride on tray (and be shorter, easier to wire and visible) to and from one row to the other row without having to go underground.
ELECTRICIANS PREFER THE STRAIGHT ENTRY INTO BOX.
Using smaller boxes is a benefit when mounting to tray not only because the tray width is limited (in this case to 12”) but also because circuits travel shorter distances to smaller boxes. True, above ground distribution is an inconvenience for the lawn mower, but the improved site circulation, lack of mud, lack of fall hazards, reduced number of heavy equipment vehicles and other effects of“trenched earth” are conspicuously absent on a site where cable tray is the rule for wire management, not the exception to the rule.
THIS CABLE TRAY WILL CARY 250KW WORTH OF DC CIRCUITS
Electricians space conductors in tray in order to benefit from the open air temperature coefficient that reduces the amount of copper required to acheive the same circuit resistance calculation as a conductor in a conduit in a trench buried under utility sand, warning tape, clear fill, top soil and landscaping because of the heat that the conductor emits inside the conduit. Savings on copper alone can amount to $1,000 to $5,000 per MW DC. In this case, the electricians are segregating the inverter home runs to the one side of the tray so that they can freely fill the other side of the tray with the smaller sub-array wiring (which is not by code required to be spaced apart). They may install a separator to insure that the smaller conductors to not creep over onto the the larger conductors which require complete expsure to fresh air according to NEC.Cable Tray can span up to 20’ and remain cost effective for solar projects. The project above has the tray (pictured) spanning 13’ from one mounting hardware column to another. The tray is supported by a bracket that can be procured from any number of vendors. The bracket detail shown on the detail below is suitbale for a schedule 80 steel pipe that supports a torque tube slew ring. In this case availability of a vertical support for the cable tray is provided by the mounting hardware.
DETAIL SHOWING SEPARATE TRAYS FOR SUB-ARRAY WIRING AND INVERTER HOME RUNS, RUNG SPACING DIFFERS PER TRAY.
Depending on the application, whether by tracker, fixed tilt, carport, roof mount or pole mount- cable tray opportunities to gain free support off of mounting structure often seem to be available for scrutiny, resolution and execution. The best support for a cable tray is often the ballast block that comes with the mounting solution and often it is the driven pier that has been cleared by the structural engineer to act as a dual purpose solution.
CABLE TRAY ON THE ROOF OF AN ELEMENTARY SCHOOL...
The ability of tray to collect conductors from under solar panels is perhaps overlooked as so often we see projects pulling hundreds of feet of cable through conduit and loading those conduit runs on pipe piers and requiring the additional labor to install thermal expansion joints, couplings, elbows and other fittings just to deliver a few pairs of #10 wire to a combiner box. Cable tray is a reliable, durable alternative to conduit and a superior cable management system compared to “trenched earth”.

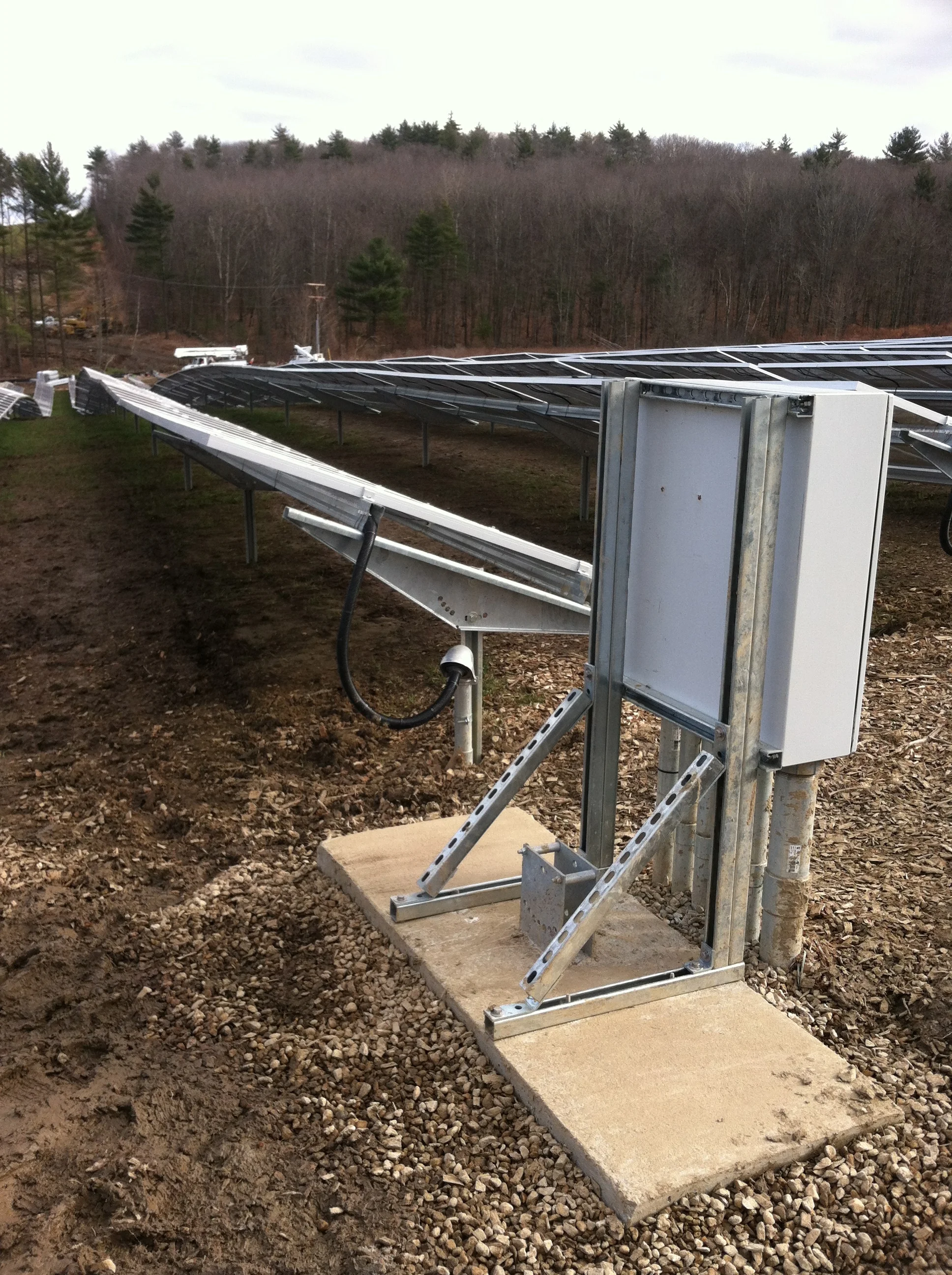
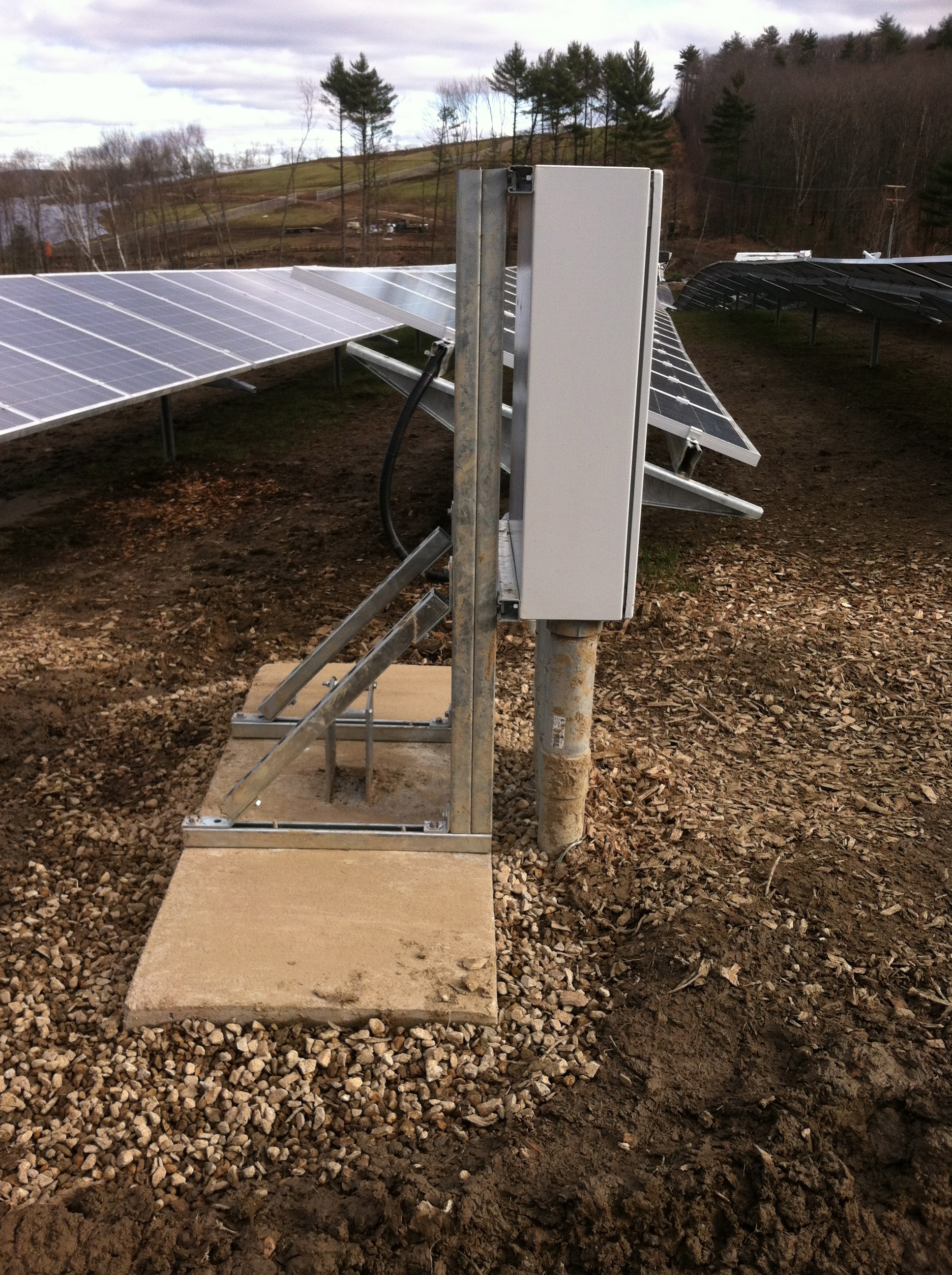
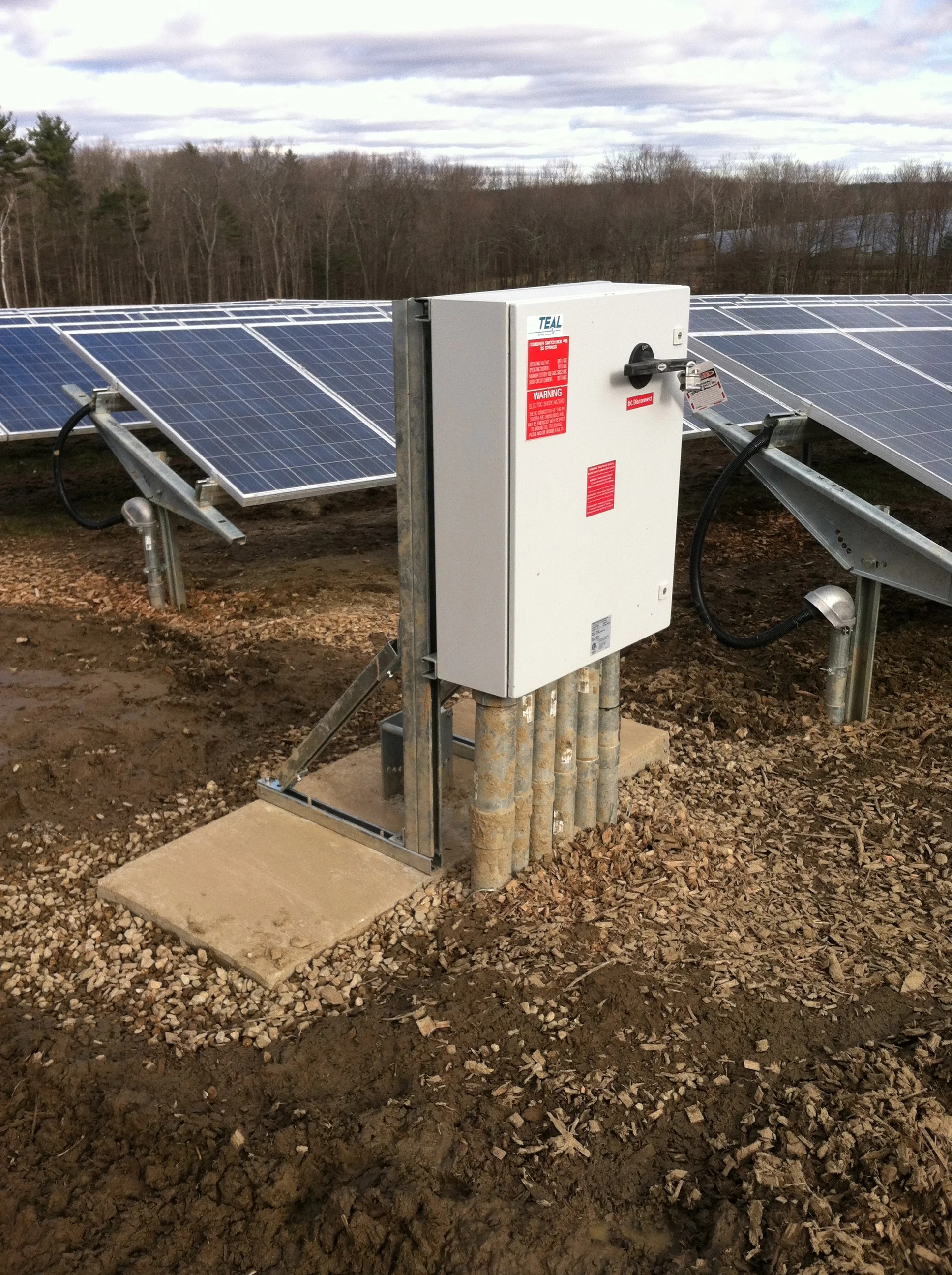
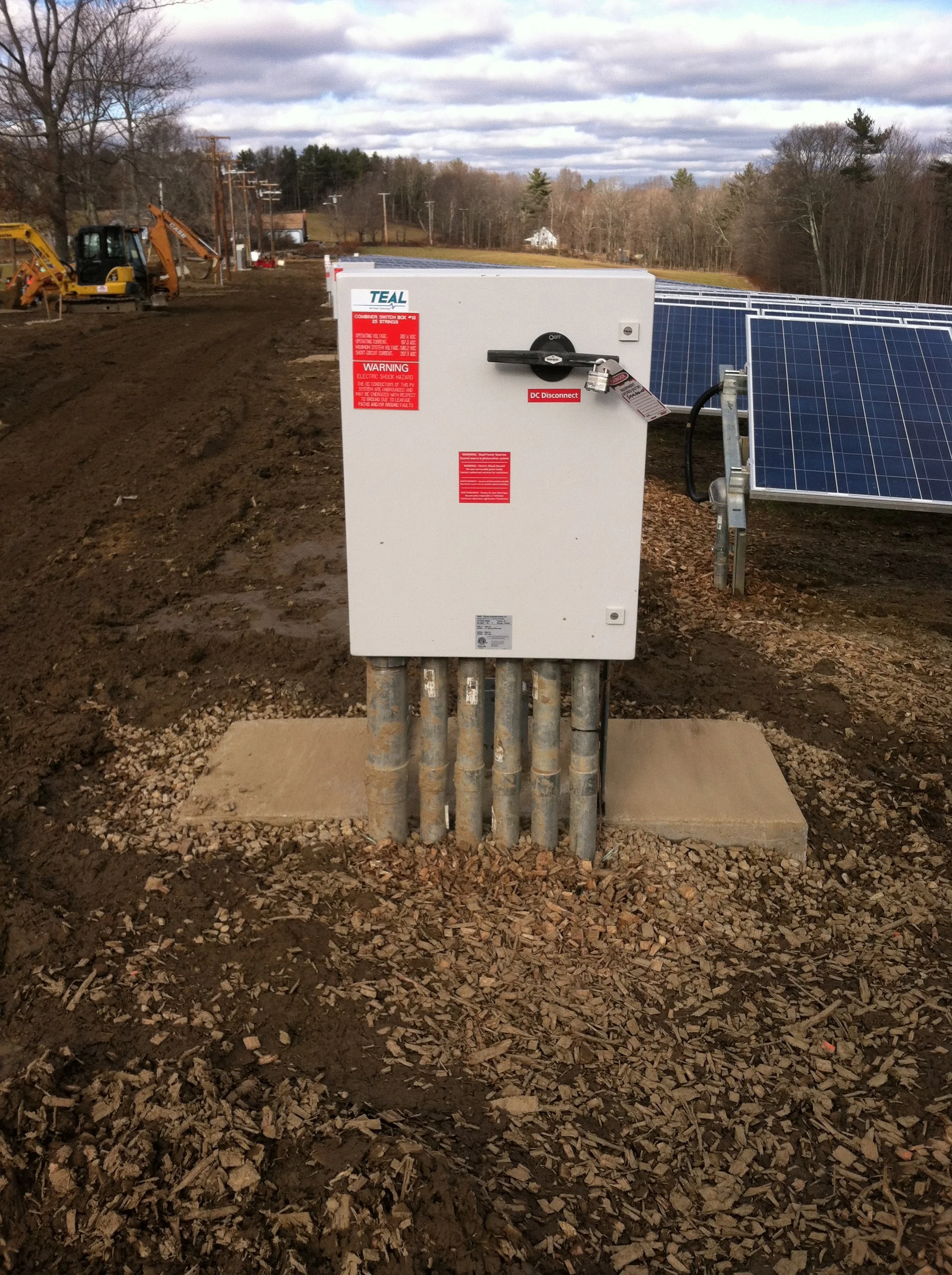
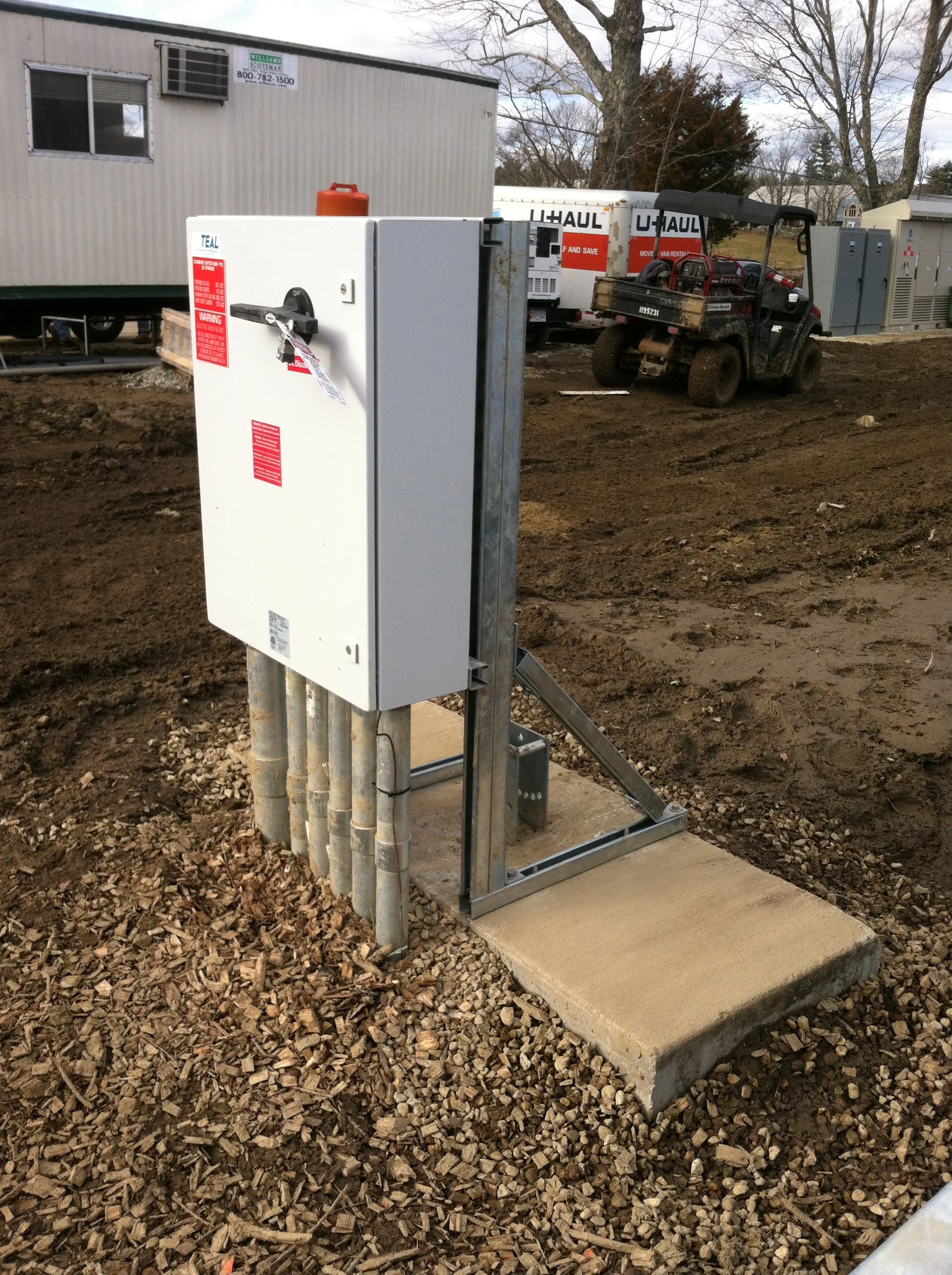
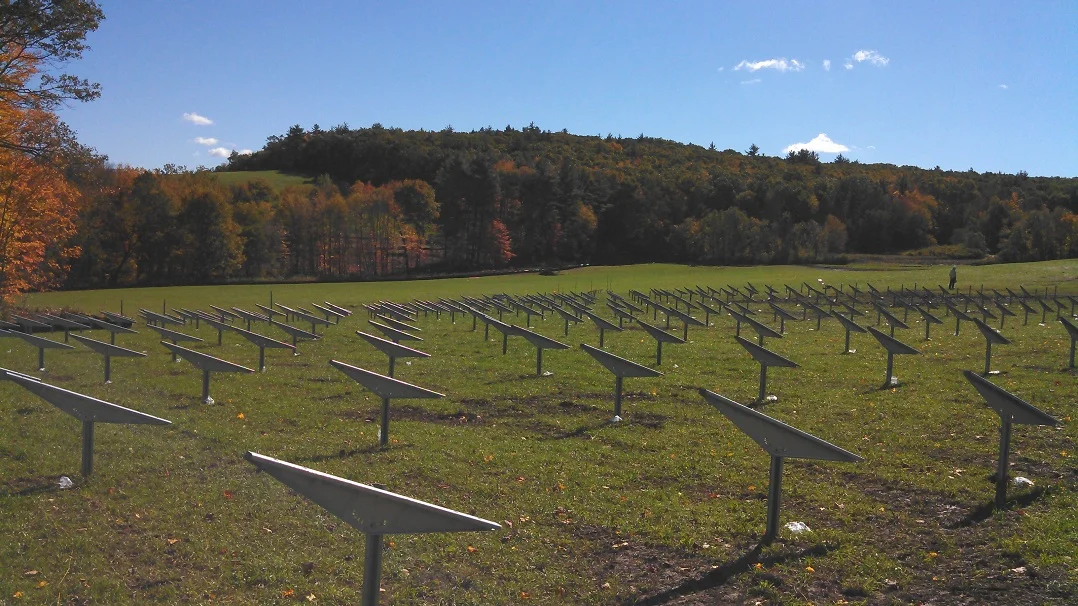





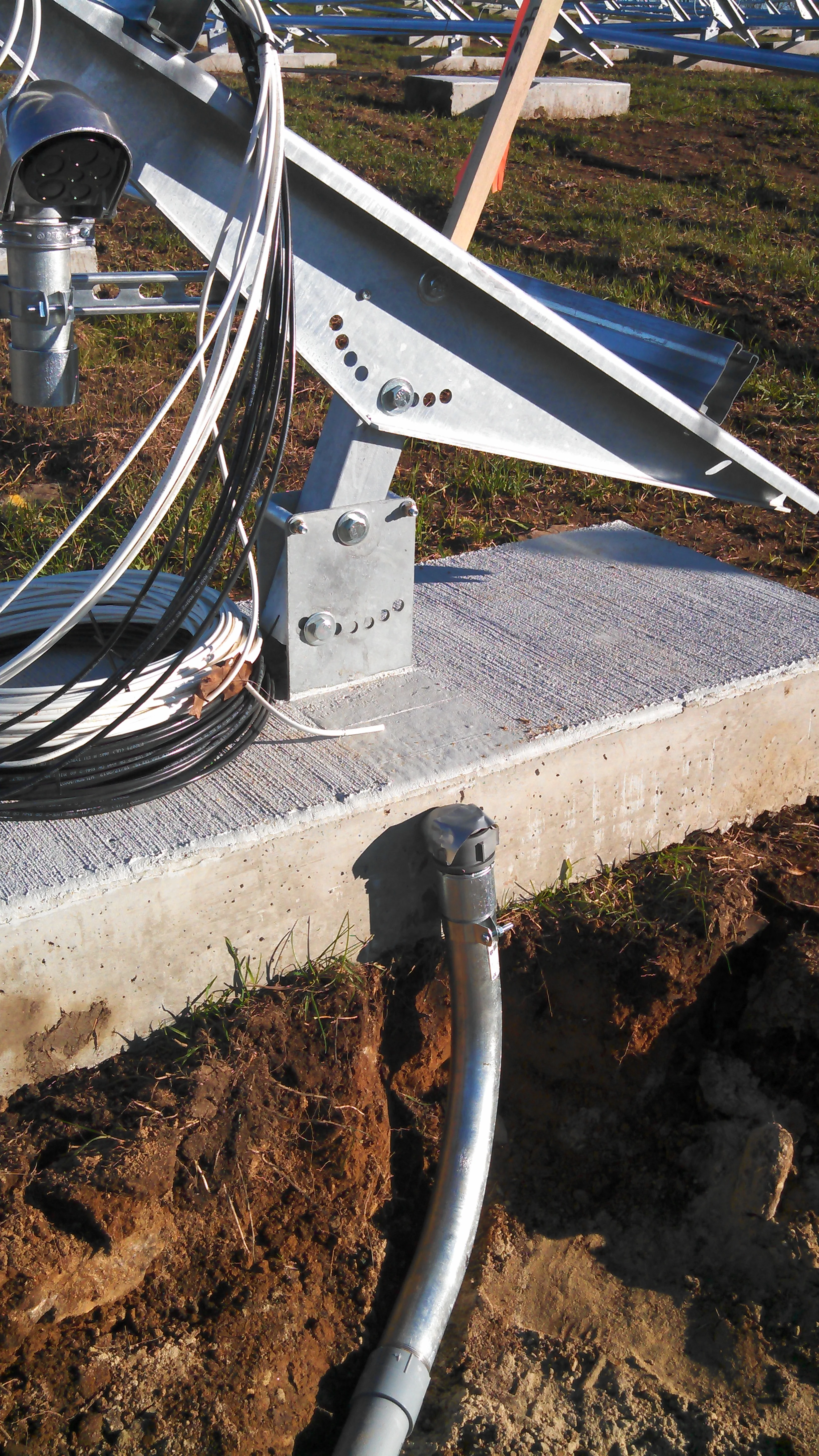
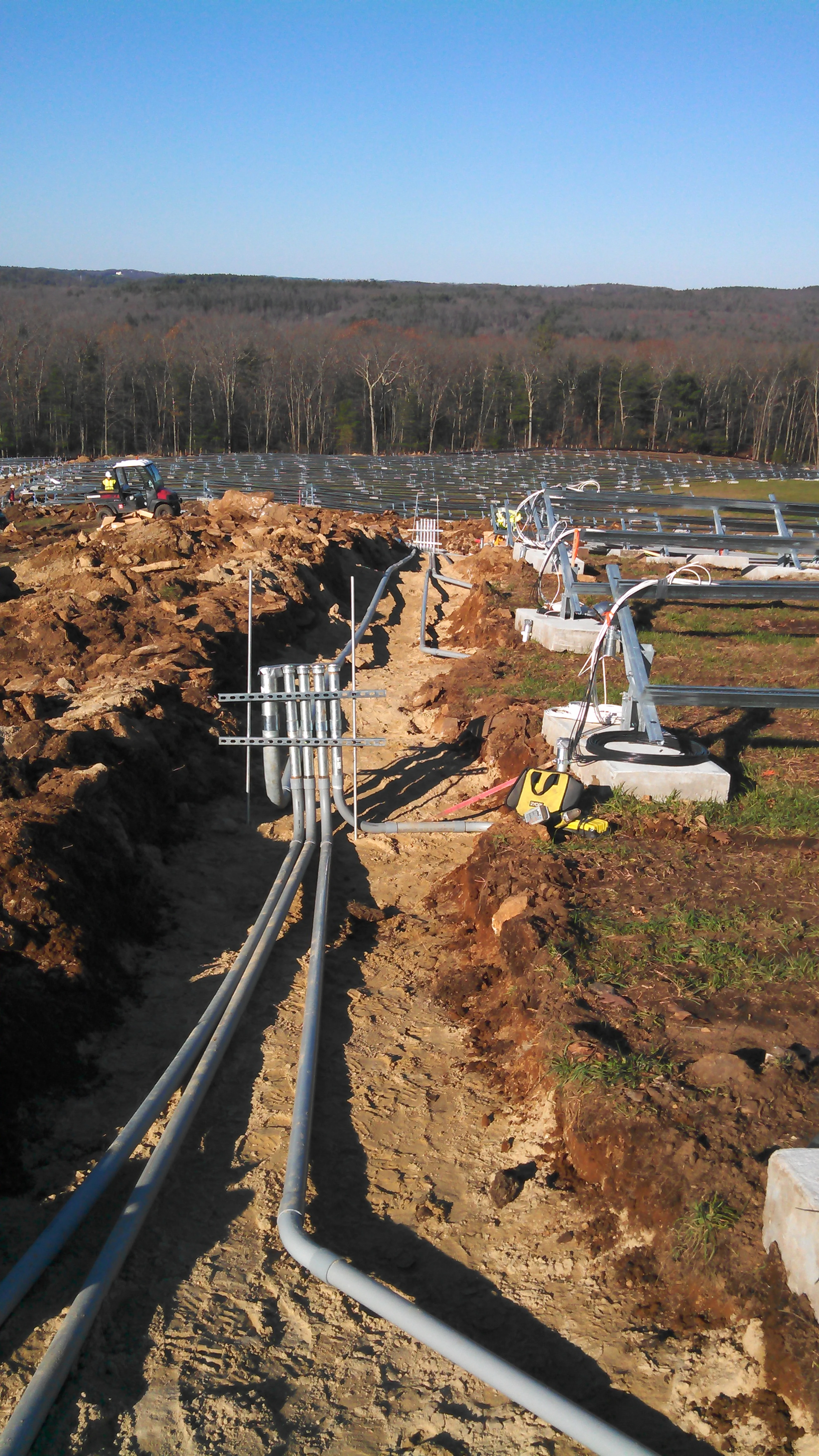

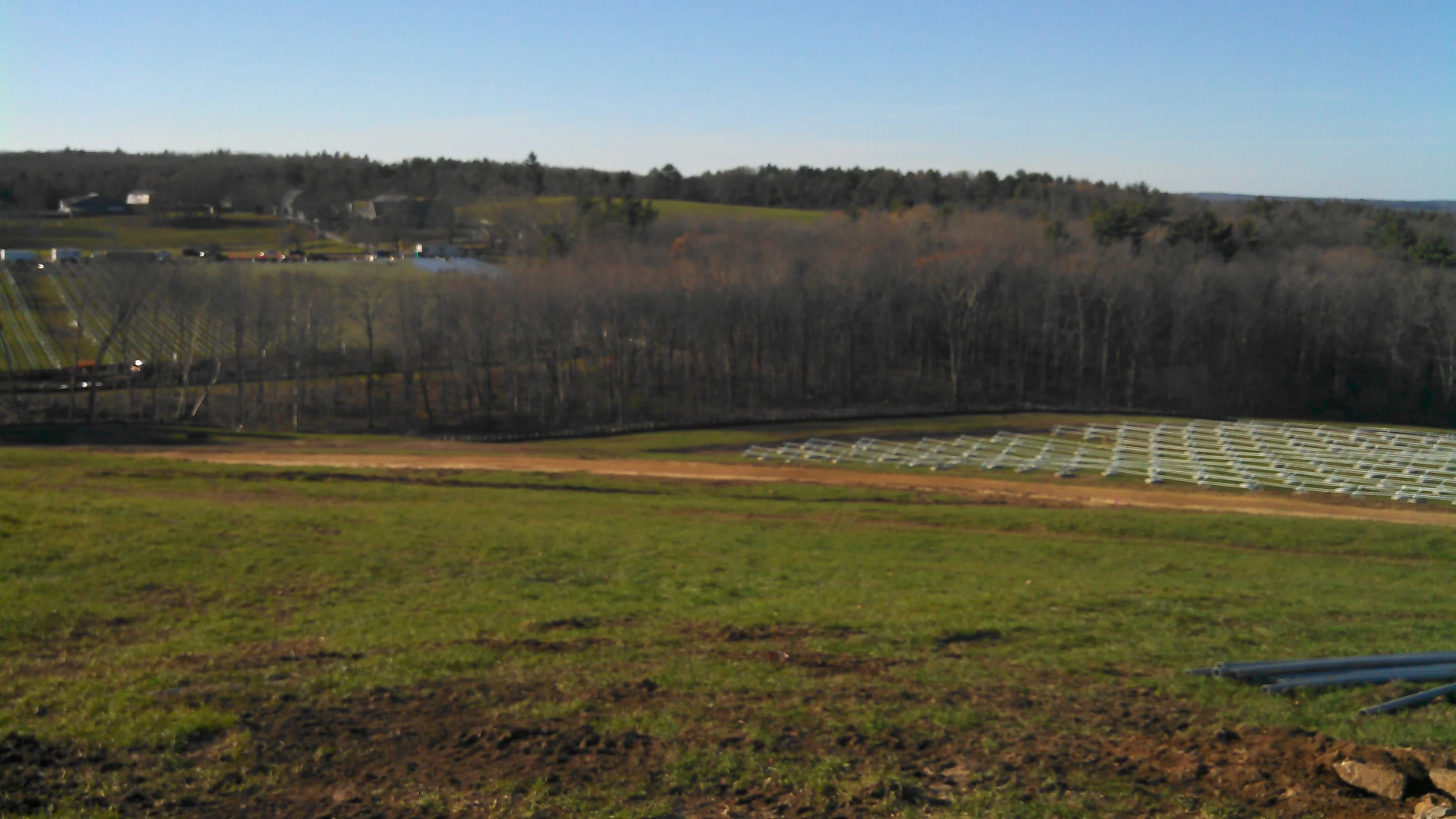

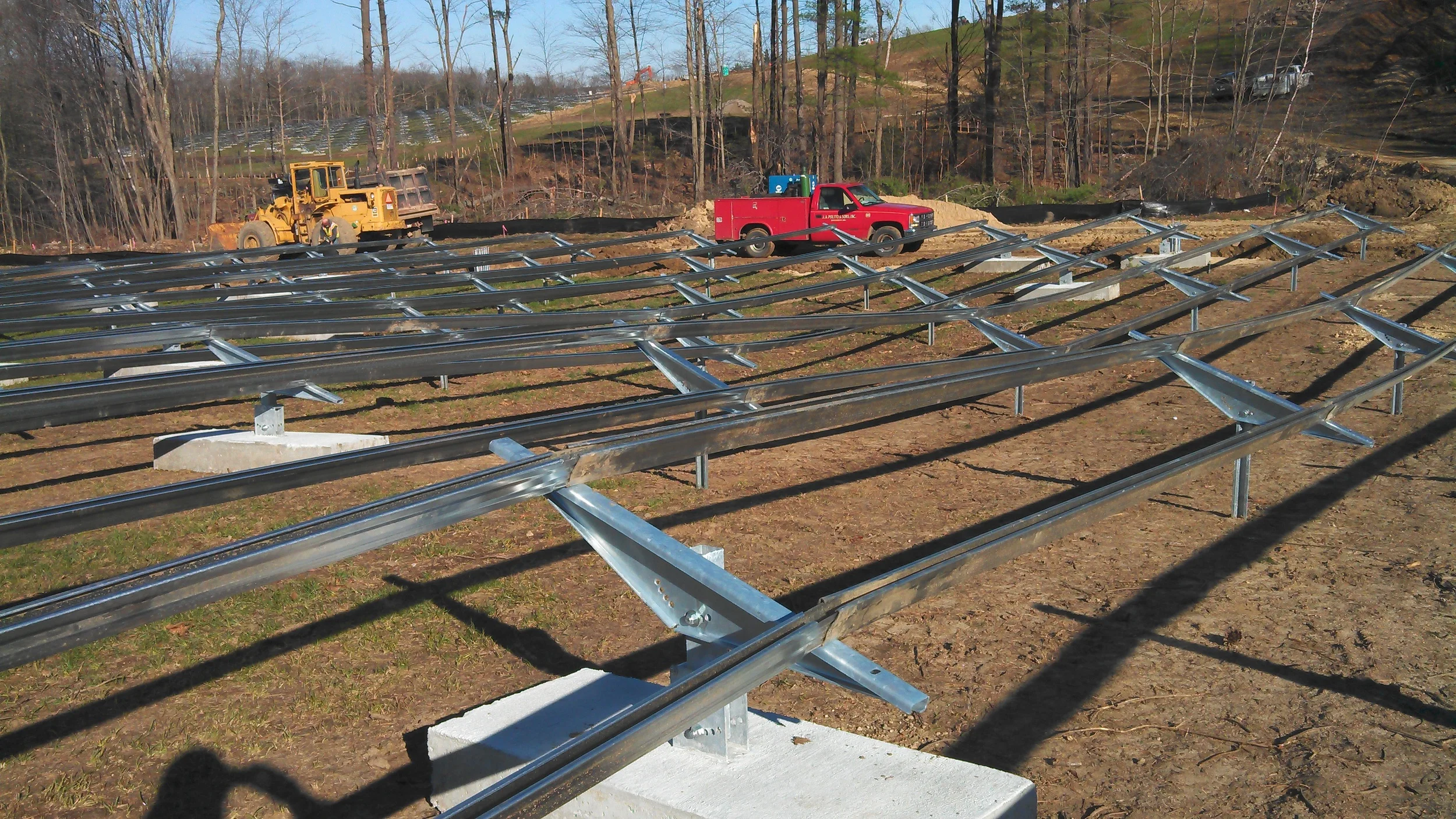




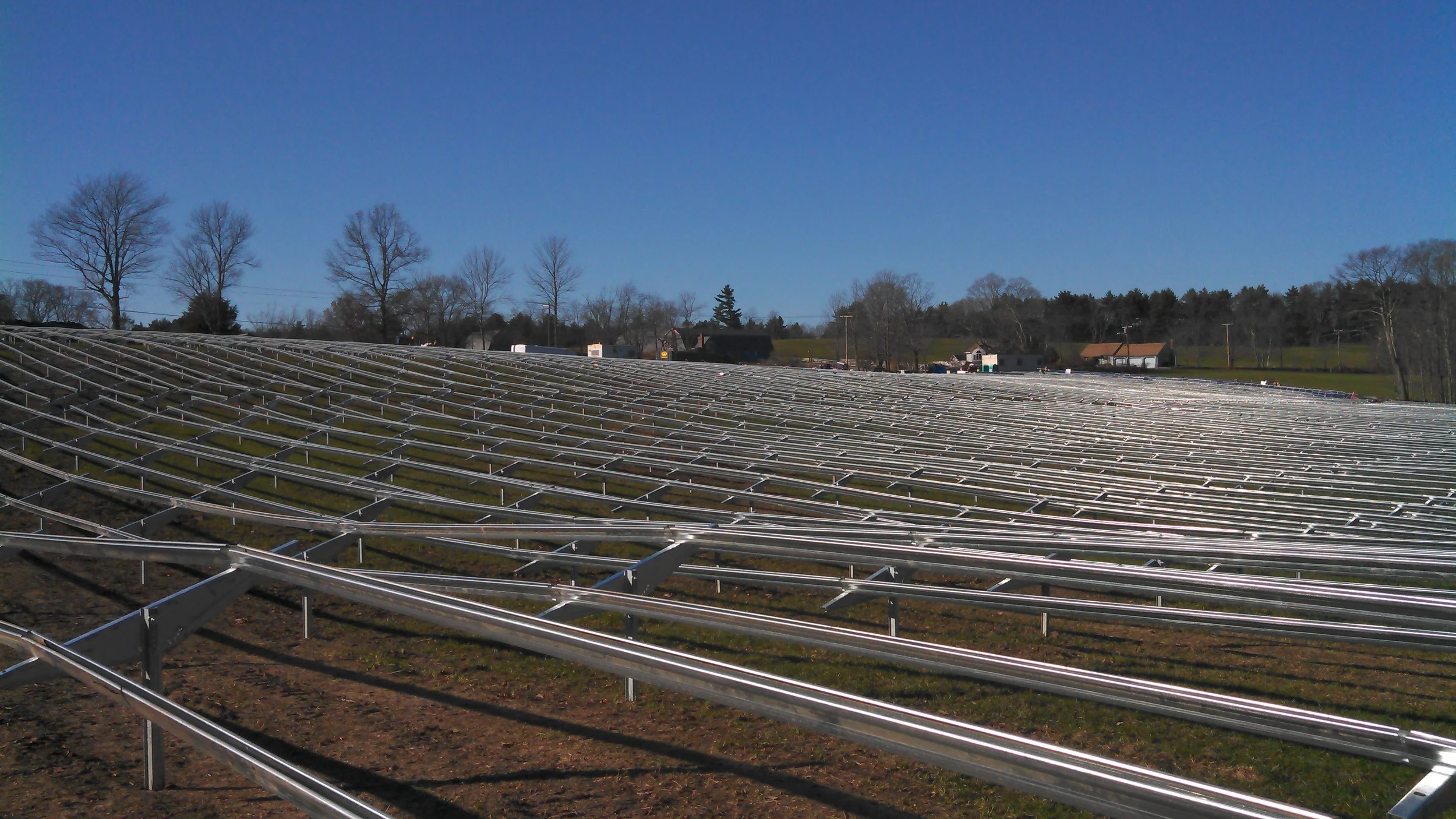
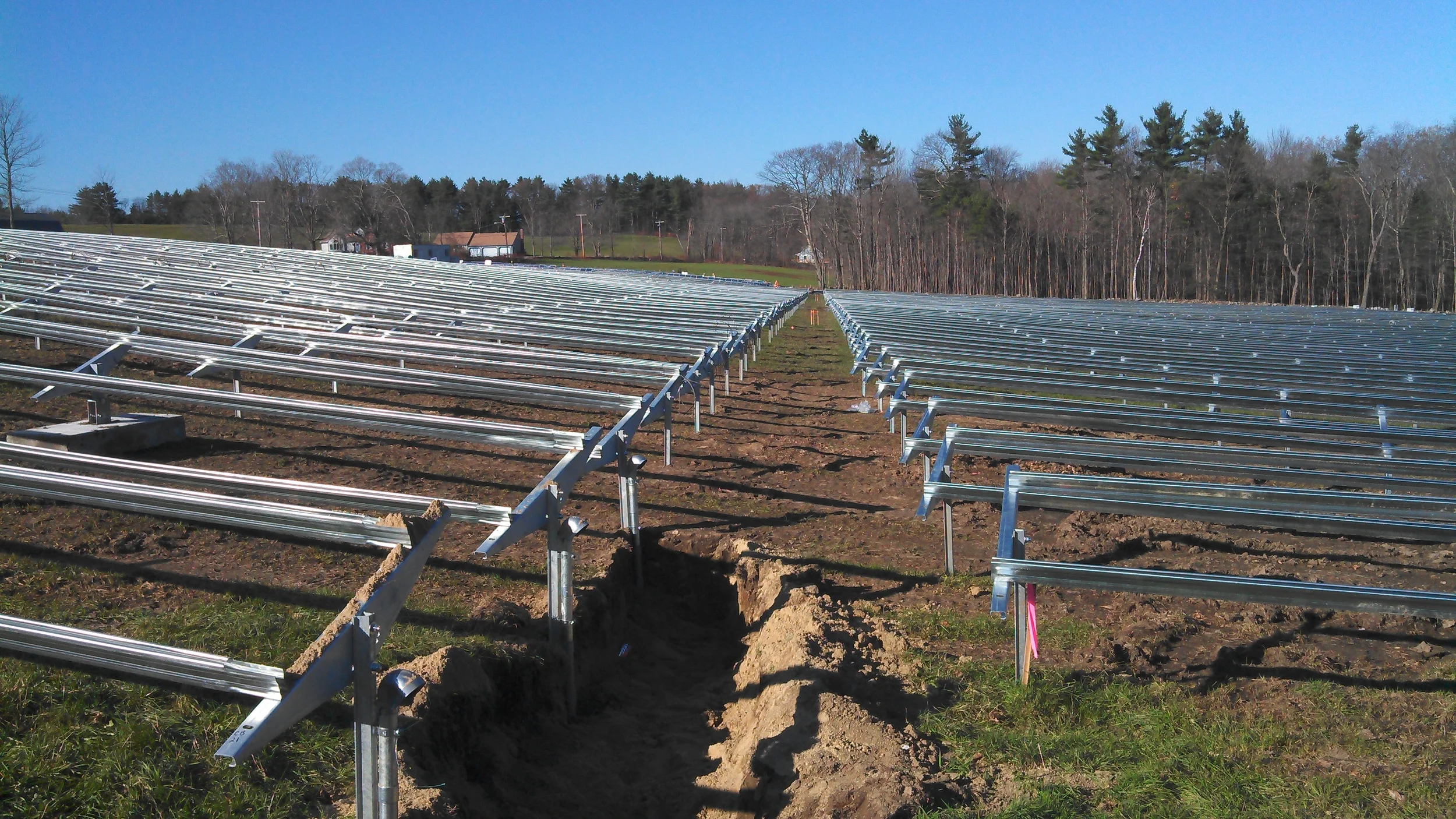
